Interview – Novel and sustainable wellbore scale removal by Blue Spark Energy
In this interview, Blue Spark Energy CEO Todd Parker describes their scale removal technology and how it helps maintain productivity in geothermal fields.
Wellbore scaling has been a perennial challenge in geothermal steam field management. When left unchecked, scale can drastically reduce the productivity of a geothermal well. Conventional scale removal methods remain expensive and unreliable and may even cause damage to the casing.
Probing for a more effective solution to this problem in the geothermal industry, we spoke with Todd Parker, President and CEO of Blue Spark Energy, a company that has developed a technology for the safe, efficient, sustainable, and cost-effective removal of wellbore remediation. With a long history in oil and gas, Blue Spark Energy has completed operations in geothermal over the past few years, with more in the queue for the remainder of 2023 and beyond.
Can you tell us about the BLUESPARK® technology and the issues of the geothermal industry that it seeks to address?
BLUESPARK® technology uses the principle of high-pulsed power. We take a small amount of energy and create a high-powered event downhole, utilizing the existing wellbore fluid, using basic physics principles combined with advanced technology to transform electricity into high-power pressure waves.
Our downhole device produces high-power pressure waves which propagate through the wellbore fluid and enter the scale. Depending on the scale’s ultimate compressional strength, they may break on impact. As the high-pressure wave travels through the material, it causes micro-fractures to be created.
When the high-power pressure wave reaches a dissimilar material, such as casing or formation rock, it acoustically reflects depending on the properties of that material. This reflection creates strong tensile forces that, when they exceed the tensile strength of the brittle material, cause it to separate and break away.
Our technology is designed for the difficult challenge of removing scale that accumulates and causes flow impediments in downhole wells, but without causing any collateral damage that compromise well integrity. This is a chemical-free process that simplifies the overall operation making it a convenient solution for common geothermal scaling issues. As the process only requires electricity, it can be a sustainable zero-emission solution is scenarios where renewable electricity is available.
The geothermal industry has had many challenges over the past years related to salts, scales, and fines that can restrict fluid flow. Scale is one of the most predominant challenges, costing the geothermal industry a great deal of money because of lower production rates and power generation obligation fines. There has not been a clean technology solution for this problem until now.
Due to the lack of a clean and convenient solution for well scaling, there are many operators that have let their wells scale closed. The result is that the operator drills a new well at the cost of millions of dollars. With our technology, we can bring some of the brownfield wells back online and potentially change their capital programs by giving access to some legacy wells.
How does your technology compare to conventional scale removal methods? Are there limitations of the more traditional methods that your technology can address?
Conventional processes (not technologies), whether chemical or mechanical, are very hard on the wells and have limitations. BLUESPARK® technology adds a third method to remove brittle scale from geothermal wells.
Chemical methods use a specific chemical for a specific scale. When there is a perfect match, it works very well. However, mismatches can result in no effect on other scale types or undesirable chemical by-products being produced, which may make scale and production problems worse.
Mechanical methods use a scraper or bit to scrape the scale from the surface; this method can be effective but is limited to only the contact area of the bit and does not remove the scale that may be accumulating in the flow path outside the well.
BLUESPARK® technology uses high-power pressure waves that exceed the mechanical strength of the brittle scale material, breaking it away from the casing. These high-power waves also propagate into the fluid flow paths beyond the surface that can be reached by mechanical methods breaking up brittle scale and debris.
The high-pressure wave is indiscriminate on the scale type as the method is based on the magnitude of the high-pressure wave exceeding the material properties of the brittle scale. The removed scale is broken into smaller pieces that can either remain in the well or be circulated out, similar to mechanical methods.
Is BLUESPARK® technology more appropriate for removing specific types of scale? Is there a maximum thickness of scale for the technology to be effective?
To date, we have removed 39 different types of scale worldwide in different wellbore environments using BLUESPARK® technology. Our technology can remove multiple scale types in a single operation – we design and optimize based on the primary scale type and scale thickness within your well, as well as the fluid density and wellbore design.
For cased wellbore applications, the only limit to scale thickness is the ability of the Blue Spark tool to enter the wellbore, as it needs to be beside the location where the scale is to be removed. Our technology needs to be able to gain access to the problem, meaning our pulse point needs to be beside the blockage for us to remove the impediment. If we cannot get beside the problem, Blue Spark cannot address the blockage.
Blue Spark has continued to advance the technology by also shrinking it to allow it to be used in various well sizes. Initially, the tools were more than 4” in diameter but have been reduced to 2 1/8”, which allowed for passing into smaller profiles.
We must also ensure that the amplitude of the high-power pressure wave exceeds the scale mechanical properties as the wave degrades with distance from the tool. For most scale types, the effective treatment penetration is several inches from the tool source.
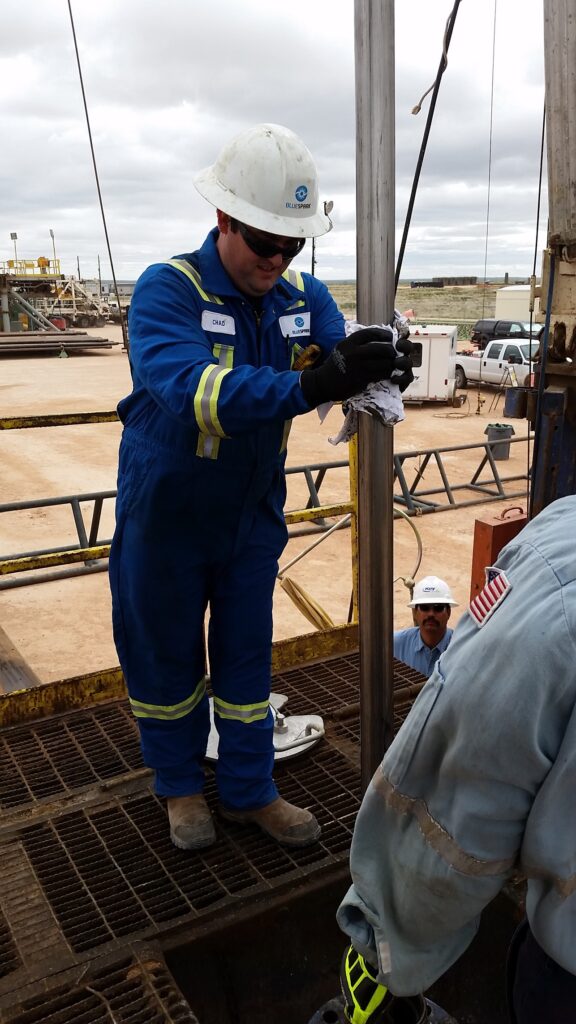
How does your scale removal process maintain well integrity?
BLUESPARK® technology creates a high-power pressure impulse that doesn’t compromise well integrity due to the nature of the two physics principles that it utilizes.
The first principle is a reflection of the wave related to differences in acoustic impedance. The contrast of impedances between brittle scale and metal casing results in most of the high-power pressure wave being reflected. This greatly reduces the amount of energy passing through the casing, thus maintaining the integrity of the well.
The second principle is due to the material type. Ductile metal casing and elastomer seals have plasticity, which allows them to absorb the short-duration, high-pulsed power pressure wave without any permanent deformation. These ductile metal materials are unaffected by the BLUESPARK® technology and can be used in various areas of the completion, such as perforated casing, slotted liners, sand screens and completion devices such as valves.
Given your company’s history in oil and gas, how has your technology adapted to the high-temperature and pressure conditions, as well as the corrosive fluids, of geothermal wells?
This is a great question and one that may surprise some people. We have been treating injection and water wells for many years and have extensive experience removing scale and blockages in water environments. The knowledge and experience we have in treating disposal and injection wells is something that we can bring to the geothermal sector.
Most of the operational issues can already be overcome by our technology, except currently for operating at very high temperatures. BLUESPARK® technology has continued to be improved for increased temperature rating. From the initial prototype at 60 °C, our technology is now commercially available for use at 130 °C. There are also ongoing product development efforts to go to higher temperatures to accommodate the unique needs of geothermal wells.
There are operators who are looking at our technology and will be quenching or cooling the treatment zone for us to operate within our temperature rating. We also have a few companies that want to invest in us to help develop the technology to be used in higher temperature ranges.
As we deal with high-pulsed power, there may be operational wells that we may never be able to operate in due to the practice of flash to steam, as we have capacitors and technology that could be impacted by extreme heat. But, we will always be able to address the concerns on the injector side, as well as the producers where they are able to cool the zone.
We continue to innovate and adapt our technology to meet the conditions in geothermal wellbores. As the geothermal market is quickly evolving, we understand the need to transition technology from other sectors to geothermal. Blue Spark Energy remains dedicated to educating and encouraging the energy industry, whether it be hydrocarbon or geothermal, to embrace change and adopt cutting-edge technologies, ensuring a sustainable and prosperous future.