Scientific approach to well design powers Fervo Energy’s Cape Station
Deliberate well design, continuous innovation, and collaboration with industry partners is paving the way for the largest enhanced geothermal systems project.
Beaver County, Utah may, at first glance, seem an unlikely hub for breakthrough technical and commercial innovation in geothermal energy. It lacks visible hot springs or geysers, and its remote location is not obviously conducive to supporting a large-scale logistical operation. However, geothermal startup Fervo Energy sees vast potential to generate commercial-scale geothermal energy in this remote valley nestled between three mountain ranges in southwest Utah.
Fervo’s private Cape Station enhanced geothermal systems (EGS) project sits just a stone’s throw away from the U.S. Department of Energy’s Frontier Observation for Research in Geothermal Energy (FORGE). This proximity provided solid benchmarks that Fervo used to conduct geothermal exploration for a multi-gigawatt geothermal power development. Armed with lessons from their previous commercial demonstration project – Project Red – in Nevada, Fervo set out to break records in Utah with a deliberate scientific and technical approach to well construction, design, and optimization at their first large greenfield development.
It is in this remote valley that Fervo plans to design, construct, and operate the world’s largest enhanced geothermal power facility to demonstrate that geothermal energy is a scalable and cost-effective solution ready for widespread deployment today.
Remote location, hard rock, and heat pose challenges
Even with the benchmark data from FORGE and experience with horizontal well drilling from Project Red, Cape Station presented a series of new challenges that required an innovative approach to logistics, project management, technology, and well optimization. Fervo set a high bar for success from the start; by the end of phase one alone, they will have drilled more than 20 wells.
From a technical standpoint, Fervo’s primary challenge consisted of drilling EGS in a remote area. Equipment must not only penetrate a difficult granite formation but also withstand temperatures on the upper end of the spectrum conventional drilling equipment can handle. Hard rock and abrasiveness characterize the granite formation, and bottomhole temperatures could reach up to 450°F (232°C).
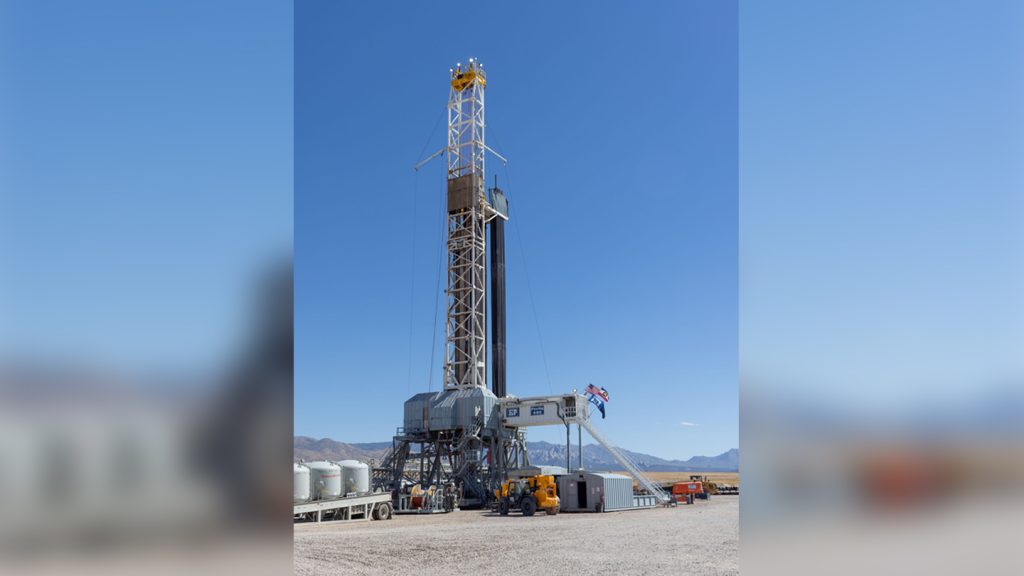
Deliberate, focused efforts break records
Prior to FORGE and Cape Station, the large-scale commercial deployment of EGS had been a pipe dream. But not only did Fervo successfully drill wells, it hit its 30-day well time milestone – one that they didn’t expect to achieve until deep into field drilling – on its third well. Now, with more than 15 wells drilled, Fervo has dropped its well time to sub-20 days. Compared to Project Red, Fervo achieved a 70 percent reduction in drilling time.
Fervo’s Project Red in Nevada provided important lessons that have applied to Cape Station. The drilling team was able to capitalize on learnings from Project Red by optimizing the well design to ensure that all well construction objectives could be satisfied whilst realizing greater operational and cost efficiencies. As Fervo continues to de-risk operations, it will further optimize well designs to capitalize on learnings picked up along the way.
The prioritization of a deliberate, focused effort geared towards on-bottom drilling optimization and a scientific approach to changes also helped Fervo achieve its goals. The operator drew from approaches pioneered by Fred Dupriest, a former chief drilling engineer for ExxonMobil who provided instruction for the drilling team at FORGE [1]. Dupriest’s approach emphasizes the use of physics to identify and reduce performance limiters. Fervo applies Dupriest’s approach not only for drilling optimization, but also to the overall well construction process to understand where optimization opportunities exist. Through this method, Fervo identifies potential limitations and engineers those limiters out of the way.
Fervo also applied a structured, deliberate continuous-improvement approach to how it makes changes in its EGS wells. The operator acts deliberately and intentionally as it tests and evaluates operational variables to achieve desired outcomes. The desire to be intentional and more predictable drives Fervo’s approach to how it makes well construction decisions, what tools they select, and what equipment they choose, such as liner hangers and cement slurries.
“It’s a mindset,” said Kareem El-Sadi, drilling engineering lead for Fervo. “If you take this deliberate, calculated approach, you’re getting it right the first time, and you’re achieving ROI faster.”
Oil and gas service companies provide critical technologies, services
Traditional oil and gas operators shy away from ultra-high strength rock, but for Fervo, the ability to target these formations would prove crucial. As the leading new operator in the geothermal energy space, Fervo has leveraged relationships with service companies to help improve upon its well design and approach.
Fervo and Halliburton first collaborated with liner hangers and cement that would ensure a high standard of well integrity. The VersaFlex® liner hanger system helped ensure Fervo would meet its long-term production targets by providing an engineered liner solution with industry leading operational and isolation capabilities to handle the severe conditions.
Halliburton also engineered a non-Portland cement blend to help ensure long-term well integrity. Fervo began with a very conservative cement design but realized they needed a new approach because of the high temperature of EGS projects. Conservative cementing formulas can be expensive. Fervo reduced costs by collaborating with Halliburton to optimize the slurry design for bottomhole circulation temperatures.
“We’ve had a lot of progress on cementing, both in terms of achieving our primary cement objectives and demonstrating that the wells, post-cementing, have the integrity that we need to complete them the way we intend,” El-Sadi said. “Working with Halliburton has provided a very quick turnaround time in terms of redesigning slurries and changing our plans as we learn more about the wells. There is not a lot of lag time between seeing an opportunity to improve and then actually closing the gap to yield the improvement.”
After the success of the liner hangers and cement, Fervo and Halliburton began to collaborate on other parts of the Cape Station wells to include Halliburton’s Baroid drilling fluids.
“We’re using a scientific approach to optimize well construction. Halliburton’s expertise in the chemistry of cement and drilling fluids and the physics of mechanical liner hangers has been a value additive to Fervo’s goals,” El-Sadi said. “Halliburton’s commitment to service quality is also a great fit for Fervo’s goals.”
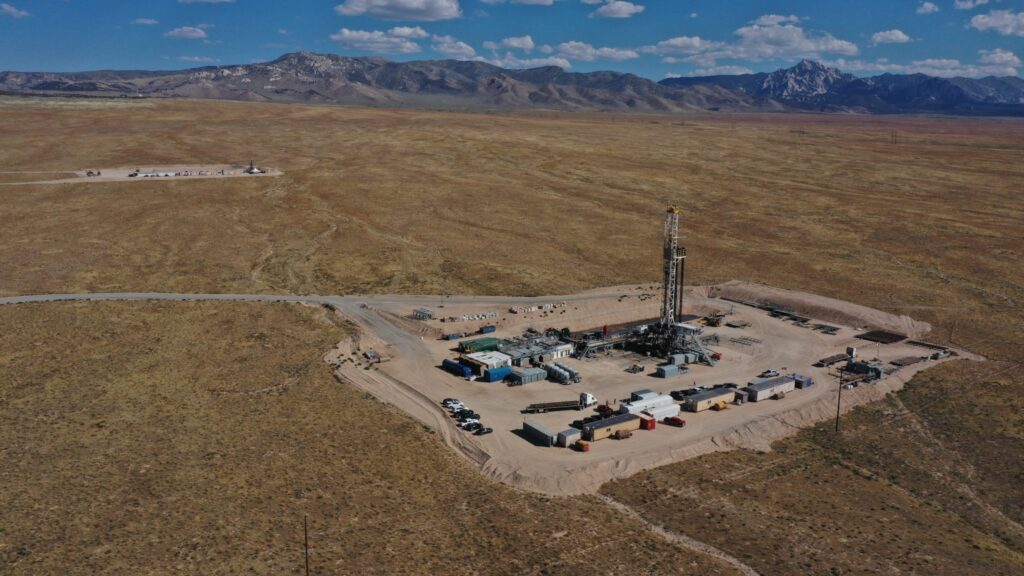
Optimize logistics to improve efficiency and reduce costs
The remote location of Cape Station did pose logistical challenges for Fervo. Regardless of the supplier, cement slurries, liner hangers, and other products had to be shipped from distant locations to Beaver County. Cement jobs required careful planning due to their quick turnaround times.
The Halliburton team helped optimize logistics to minimize the number of trips from Bakersfield, CA where it mixed cement slurries. In cases where Fervo batch-drilled wells, it could load out cement for multiple wells instead of sending trucks for each job. This allowed Fervo to lower emissions, safety exposure, and even rig time, as it could keep the required supplies on location to immediately begin the next phase of the project.
Continuous refinement at Cape Station
Fervo’s methodical approach to drilling geothermal wells includes planning for contingencies and learning from challenges. They have proven the value of upfront modeling to address edge cases and plan for uncertainty, which helps ensure success during execution.
Fervo also evaluates previous project performance to identify opportunities for optimization. The decision to use Halliburton’s Bariod drilling fluids, for example, stems from a desire to further optimize drilling fluid design to effectively mitigate challenges observed in the granite interval. The ability to understand challenges, identify root causes, and address them in a way that is both sustainable and cost-effective, while ensuring long-term efficiency, requires continuous effort.
Halliburton engineered custom fluid solutions to maximize wellbore value for Fervo. The company introduced technology and services that helped Fervo reduce surface consumption by more than 80 percent and decrease defoamer usage in the production section by more than 50 percent.
Halliburton will soon collect samples from highly reactive clay zones when they are drilled for analysis and proper inhibition mechanisms. This process will allow Fervo to predict and prevent risks before they occur based on analytical and operational insights. For program continuous improvement, new lubricants are in development to mitigate future foaming risks.
“We’re building on that critical first well process and global expertise and support from Halliburton that we’ve seen with liner hangers and cementing, hoping to see to the same on the drilling fluids front to help us optimize,” said El-Sadi.
The future at Cape Station involves continuous innovation on well designs to enhance productivity and reduce well time and costs. Unlike oil and gas wells, where operators drill for oil and gas and deplete the reservoir, EGS systems do not access a commodity and shut down. The potential to improve productivity lies in drilling into deeper and hotter formations and the creation of larger bore sizes. Meanwhile, Fervo will also look for ways to optimize drilling, improve performance, and reduce cycle time.
Fervo’s success at Cape Station shows there are no remaining technical barriers to large scale EGS deployment. Fervo’s advancements demonstrate that EGS can be a viable and scalable solution for 24/7 carbon-free energy. If anything, Fervo demonstrates that a scientific, technical, deliberate approach to well design, well construction, and well optimization can transfer the physics used in oil and gas wells to geothermal, even in ultra hard rock and high temperature environments. The adoption of this philosophy can unlock even more geothermal resources, not just at Cape Station but around the world.
By 2026, Fervo expects to start grid supply from its Cape Station project. It already signed two PPAs totaling 320 MW with Southern California Edison, and Cape Station may prove itself as the most productive EGS in history. [2]
“Cape Station is where EGS starts and it’s also going to be where EGS evolves and improves. We think that the area will be as consequential for geothermal as the Permian Basin is for oil and gas,” El-Sadi said.
[1] Physics-based instruction leads to huge success for geothermal drilling | Texas A&M University Engineering (tamu.edu)
[2] Fervo announces technical and commercial breakthroughs at Cape Station geothermal site (thinkgeoenergy.com)